If you want to switch to LEDs and are looking for the right product, you should know the term binning. But what is LED binning? And Why LED binning is important?
LEDs, like other manufactured products, have material and process variations that yield products with the corresponding variation in performance.
LEDs are binned and packaged to balance the nature of the manufacturing process with the needs of the lighting industry.
What is LED Binning?
LED binning is the technique manufacturers use to make sure that all the LEDs are similar in nature.
Deviations occur frequently in the industrial production of LEDs: even LEDs from the same product batch differ in their properties. The slightest alterations in the manufacturing process of LED (in regards to color temperature, lumens, and LED voltage), make it very difficult to have all the LEDs exactly the same.
LEDs tend to be similar but rarely identical.
In order to avoid large deviations, LEDs with similar performance are grouped together in so-called “bins” (containers).
For example, for LEDs to be green, manufacturers need to ensure all of their LEDs are indeed the same shade of green. The LEDs of the same shade of green are grouped together in a bin.
LEDs are placed into similar categories – bins based on similarity of –
- lumens
- voltage
- color
Lumens and color are the most important factors in LED binning.
LED Binning according to lumens is relatively simple. But Binning LEDs according to color is more complex and to understand the process you need to be familiar with chromaticity diagrams.
Why LED binning is important?
Why is LED binning important to you as a consumer?
The answer is simple: Binning systems guarantee the lighting standards of LEDs. This ensures that the same LEDs deliver the same performance – and that you won’t be disappointed with products.
In lighting industry, precise color quality is highly important so there needs to be a system that ensures color consistency. If you buy a set of LED fixtures in January and decide to order more in July, you’ll obviously want your LED arrays to match.
This is where binning comes in.
Binning is particularly necessary for LEDs with a white light spectrum, as the color temperature and brightness values can otherwise vary too much.
Do you prefer more visual demonstration, you may watch the following video on LED Binning and its importance.
LED Binning Criteria
Most manufacturers sort their production based on following binning criteria:
- Luminosity ( lumens )
- Color temperature (Kelvin)
- Voltage (volts)
- Color location (color impression when viewed directly)
The manufacturer usually specifies which bin a product class has been assigned to on the product specifications sheet. So it is worth taking a look – this is how you can find out about the assigned properties of the LEDs.
LED Binning Process
Luminosity and color temperature are the most important binning criteria that directly influence the product performance of the LED chips.
For example, to sort the LEDs by luminosity, they are measured individually and sorted into specified areas.
Manufacturers tend to develop their own binning system that matches the production results. The larger the bin, the more the values of the individual LEDs may differ from one another. The narrower the bins, the more expensive the sorting and, accordingly, the LED product.
LED Binning Based on Lumens
Binning for light output is a very straightforward linear function. LEDs are individually measured and sorted by lumen output into prescribed ranges.
LED suppliers create their own standard set of lumen bins and provide clear information on the expected lumen performance of each of their bin ranges.
So, luminaire manufacturers can easily select the bin (or set of bins) that best meets the lumen performance requirements of the light fixture.
LED Binning Based on Color Temperature
To ensure that LEDs have the same color temperature, they are sorted according to the ANSI (American National Standards Institute) standard.
It defines chromatic deviations using the MacAdam ellipses, which are also known as “Standard Deviation Color Matching (SDCM)”.
American physicist, David MacAdam showed there are regions on the chromaticity diagram that contain all colors which are indistinguishable from the color at the center of observation.
That means, that an ellipse could be drawn around a single point on the chromaticity diagram where, within that ellipse, the human eye cannot distinguish different colors.
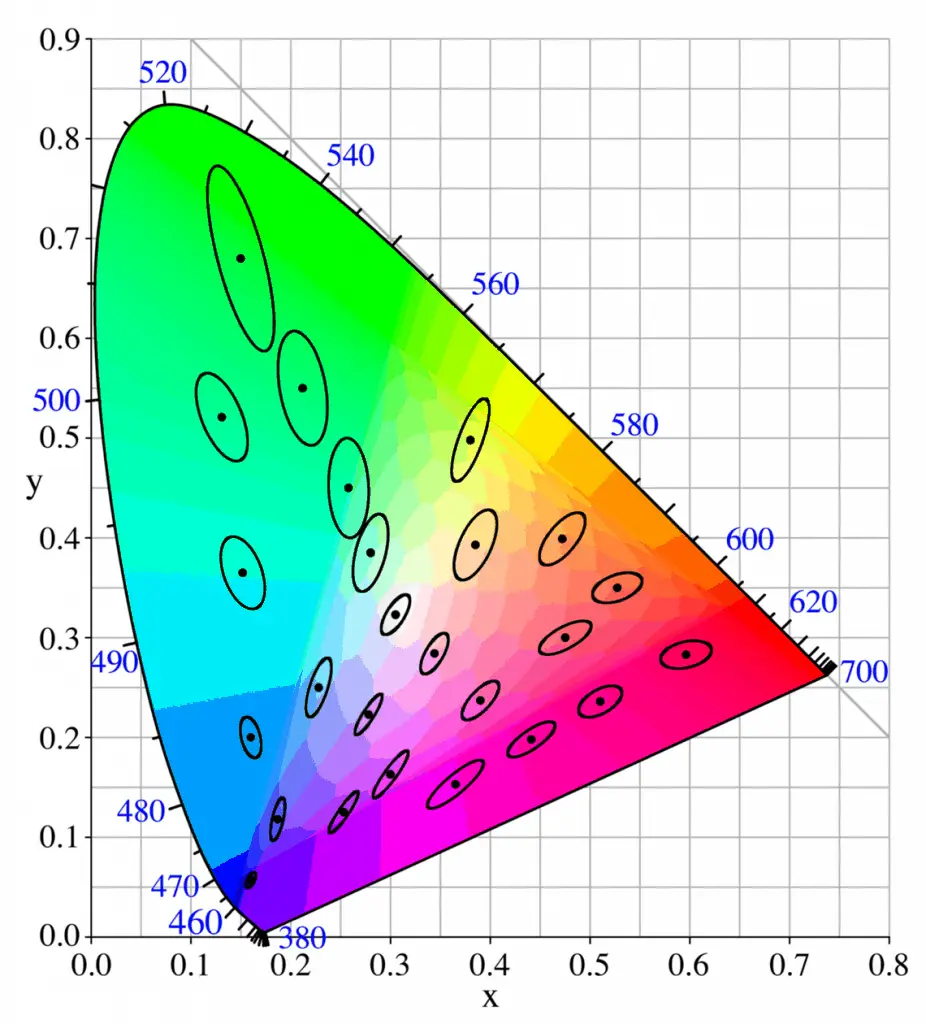
The ANSI standard recommends that the color value be within four threshold units in an ellipse. The ellipses inform the user how far, for example, the light color of individual LED chips deviates from one another.
LEDs in these bin areas guarantee uniform light colors, for example, that 4,000 K is cool white. Most manufacturers use an average of 2 SDCM.
This table should clarify the system for you:
McAdam Ellipses (SDCM) | Visibility |
---|---|
1 SDCM | Almost impossible to see a difference |
2 SDCM | Differences can be seen through measuring instruments |
3 SDCM | Less color differences visible |
4 SDCM | Color differences are visible |
5 SDCM | Clear differences are visible |
If you are more interested, you can watch the video on LED bin selection process.
In the past, the reference positions of the MacAdam ellipses were set arbitrarily and did not cover all color areas. At temperatures above 6,000 K, no MacAdam ellipse could be assigned unless the manufacturers defined their own. Fortunately, that has changed today.
Color temperatures can also deviate independently of binning, e.g. due to age or due to wear and tear of the lamp sockets.
Further deviations in color temperature
- Manufacturing tolerances ensure that the same products do not create a different color impression
- after 10,000 hours there may still be an age-related color shift
- The V Before Using of devices and covers, the original color temperature misrepresent
- In order to avoid large deviations, LEDs will be made more precise in terms of technology and quality in the future
We hope you’ve enjoyed the article, and that you’ve learned what you wanted to know about LED BIN selection.